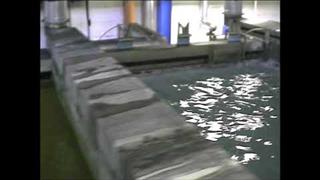
our plants
pre-treatment

Each new plant is designed according to customer specifications and to specific industrial or automotive norms.
Many plant configurations are available depending on which alloys will be treated and which will the final uses be:
Tunnel Treatment
In the field of industrial cleansing the tunnel system is the most vastly used one. In such plants, the objects are either racked on an overhead or on a floor conveyor which moves them through a tunnel where they are flushed by jets or sprays of plain water or other solutions of chemical specialties.
Spray tunnels are made for both on line and step plants with automated movable partitions needed to prevent vapours from escaping the chambers.
An accurate inspection of the objects to treat and a set of laboratory tests help in choosing the number of needed treatment stages and the right contact times in each one of them. From these originates the quality of the treated items, already from the first design steps upon which the final installation will develop.
Dip treatment in tanks
An alternative option, most commonly used in the automotive and aerospace industries, is a system developed over consecutive tanks for a liquid dip or spray treatment. Fixed on specifically made racks, the objects move from tank to tank with the aid of automated overhead bridge cranes.
As in the tunnel configuration. Here too the number of stages/tanks and the right contact times needed to meet customer satisfaction at the best originate from an accurate evaluation of test results made on the items to be treated. This is a most important step in assuring that the wanted final quality is met from the very first draft of the plant.
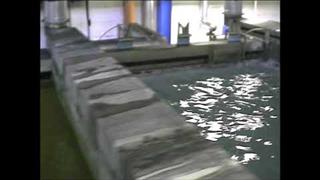